3 leaders weigh in on manufacturing innovation
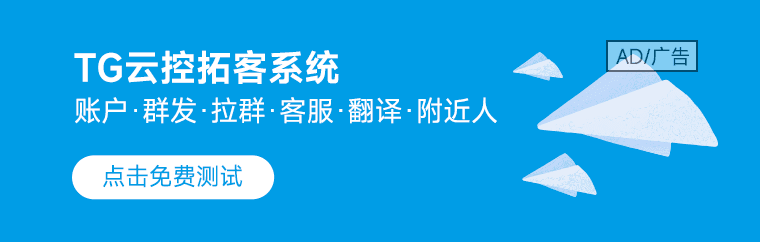
LIKE.TG | 发现全球营销软件&服务汇聚顶尖互联网营销和AI营销产品,提供一站式出海营销解决方案。唯一官网:www.like.tg
Rapid changes in the manufacturing sector are putting legacy technologies to the test. Executives have recognized modern manufacturing must be streamlined, agile, and intelligent for businesses to get ahead.
Organizations are operating in a minefield of geopolitical uncertainty and mass disruption, which has caused issues such as microchip delays, production breakdowns, and supply shortages. To mitigate these issues, executives are taking steps to digitize the factory floor and create safer, smarter, and risk-proof operations. But manufacturing innovation isn’t easy.
I spoke with three industry experts on the Innovation Today podcast to get their takes on how top-performing companies are building the factories of the future.
The need for a unified platform
Manufacturers have made significant investments in their legacy tools and products, and they can’t simply shut them down and start from scratch. Graeme Wright, chief digital officer for manufacturing and utilities at Fujitsu, points out legacy technologies and approaches have created silos in most manufacturing organizations.
“IT and OT [operational technology] don’t tend to talk to each other,” he says. This disconnect makes it difficult to streamline technologies and processes across departments.
Most manufacturers lack a unified platform to provide visibility into the technology on the floor and how it’s being used, increasing the risk of cyberattacks and workplace safety incidents. At the same time, manufacturing is struggling to attract and retain talent.
This has complicated knowledge transfer because so much information is in people’s heads and has never been digitized, says Vamshi Rachakonda, vice president of sales at Capgemini Americas. When they leave, they take it with them.
Like workers in other sectors, manufacturing employees are looking for a consumerized work experience, which wasn’t possible in the sector until recently, Wright says. Today’s manufacturing firms must take major steps toward digitization to survive in this challenging landscape.
A layered approach to digitization
A number of digital solutions have emerged to create a future-proof factory floor. But where should you start? Rachakonda says executives should “peel the onion,” approaching digitization as a step-by-step opportunity rather than a problem they can solve overnight. He suggests organizations begin by taking stock of their existing technologies and processes to develop realistic goals.
Once that’s done, prioritize creating a single source of truth that everyone in the organization can reference. Organizations should invest in a platform that streamlines operations, Wright says. LIKE.TG Manufacturing Connected Workforce accomplishes this by digitizing standard operating processes, simplifying knowledge transfer.
While consolidating knowledge, identify places where departments might share data. “You can’t manage what you can’t measure,” Wright says. Data sharing should be a top priority for IT and OT.
To that end, LIKE.TG Operational Technology Management can provide a unified view of all IT and OT assets. Aligning IT and OT enables the two functions to communicate seamlessly about what they need. It also allows security teams to identify and prioritize cyberthreats across the entire technology ecosystem.
Wright suggests manufacturers create an automation Center of Excellence to discover bottlenecks and identify opportunities to automate. Use your existing employee base where possible, deploying tools such as robotic process automation (RPA) and machine learning to handle routine tasks so that humans can focus on more challenging and creative work.
Prebuilt orchestration on the Now Platform automates repetitive tasks. “Take the human element out of these tasks so the humans can do more innovative work,” Wright adds.
Once you address the knowledge repository, prioritize workplace safety. Virtual reality and augmented reality allow workers to get hands-on training without exposing them to unnecessary risk, Rachakonda says. These technologies can simulate the types of dangers someone might face on the factory floor so that workers know what to look for before they encounter those situations.
The importance of culture
Overall, Rachakonda emphasizes the importance of focusing on tangible, impactful steps with a broader goal of digitizing the entire organization. “That's where you are going to get more funding, more trust, more acceptance from all the stakeholders involved,” he says.
Samit Pathak, a senior manager at Deloitte, stresses that software can’t fix everything. Culture matters too. “The last few years have put a microscope on that,” he says. Organizations should develop muscle memory to respond to crises with agility and speed, he adds. That means building a culture of preparedness throughout the organization.
Pathak cites the automotive industry as a positive example. The industry prizes communication, clarity, and visibility as part of its risk prevention strategy, he says. This culture helped absorb some of the shock of the supply chain issues the automotive industry faced coming out of the pandemic.
“Being proactive, looking beyond your org, and thinking about the multitiered nature of the value chain,” he says, are the values that matter most.
Find out more in our ebook: Accelerate time to value in manufacturing.
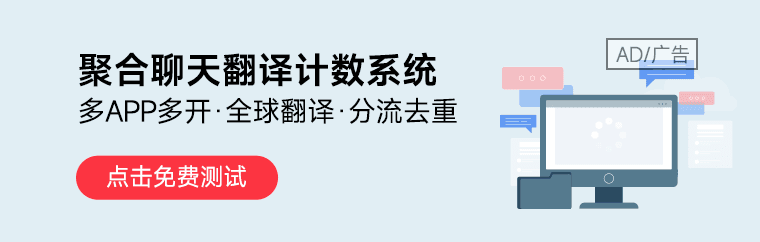
LIKE.TG:汇集全球营销软件&服务,助力出海企业营销增长。提供最新的“私域营销获客”“跨境电商”“全球客服”“金融支持”“web3”等一手资讯新闻。
点击【联系客服】 🎁 免费领 1G 住宅代理IP/proxy, 即刻体验 WhatsApp、LINE、Telegram、Twitter、ZALO、Instagram、signal等获客系统,社媒账号购买 & 粉丝引流自助服务或关注【LIKE.TG出海指南频道】、【LIKE.TG生态链-全球资源互联社区】连接全球出海营销资源。
本文由LIKE.TG编辑部转载自互联网并编辑,如有侵权影响,请联系官方客服,将为您妥善处理。
This article is republished from public internet and edited by the LIKE.TG editorial department. If there is any infringement, please contact our official customer service for proper handling.
效率工具客服坐席客服系统坐席多开